What is Aluminum PCB: Structure and Heat Conductivity
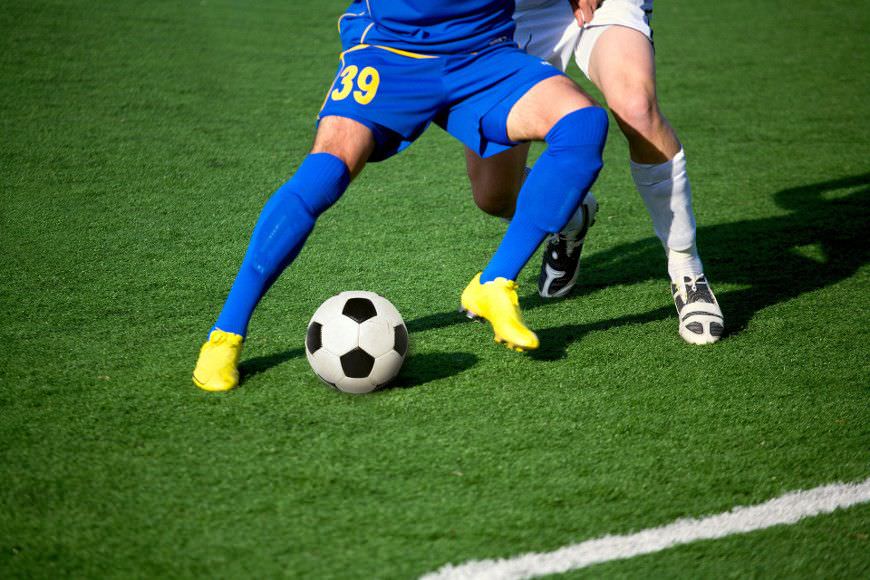
Printed circuit boards (PCBs) are essential components in the manufacturing process of electronic devices. They serve as platforms for wiring and connecting electronic components, allowing for the transmission of electrical signals and data between them. PCBs are critical components in the development and manufacturing of modern technology, and they undergo various processes throughout the manufacturing process.
One type of PCB that has gained popularity in recent years is the aluminum PCB. Aluminum PCBs are made from aluminum, a versatile metal that is commonly used in various industries. In this article, we will explore the structure and heat conductivity of aluminum PCBs and how they contribute to their performance and reliability.
1. Structure: Aluminum PCBs are typically made from multilayer structures that include various types of circuitry patterns and components. The base material is aluminum, which provides a lightweight, strong, and conductive base for the board. Copper layers are applied to create circuitry patterns, and other materials such as soldermask, insulation layers, adhesives, and conductive paste are used to create the board's structure.
2. Heat Conductivity: Aluminum has excellent heat conductivity, which makes it a popular choice for use in heat-sensitive components such as processors and power semiconductors. The high heat conductivity of aluminum allows for efficient heat dissipation and prevents overheating, ensuring that the components remain stable and reliable.
3. Thermal Management: Thermal management is crucial in electronic devices due to the high power density requirements of modern technology components. Aluminum PCBs offer excellent thermal management capabilities due to their high heat conductivity,aluminum pcb manufacturer which helps to dissipate heat generated by components and maintain their operating temperatures within safe limits.
4. Durability: Aluminum is a highly durable material that exhibits excellent corrosion resistance and durability under extreme conditions. This makes aluminum a preferred material for critical applications where it is commonly used in medical devices, automotive components, and other critical equipment. Its durability ensures that aluminum PCBs can withstand repeated use and harsh environments, providing long-term reliability and durability.
5. Cost-Effectiveness: The cost-effectiveness of aluminum PCBs is another key advantage they offer over traditional PCBs made from other materials. The use of lightweight aluminum as a base material reduces the overall weight of the device, leading to lower production costs and increased efficiency in terms of energy consumption and transportation. Additionally, the high heat conductivity of aluminum contributes to faster heat dissipation, reducing the need for additional cooling systems, which further reduces costs.
In conclusion, aluminum PCBs are a versatile and cost-effective material that offers excellent heat conductivity, durability, and cost-effectiveness. Understanding their structure and heat conductivity is crucial for comprehending their role in modern technology development and manufacturing processes. Aluminum PCBs are becoming increasingly popular due to their lightweight nature, high conductivity, cost-effectiveness, and durability. They are commonly used in small and lightweight devices such as smartphones, tablets, computers, and other electronic gadgets. Additionally, aluminum's biocompatibility makes it a preferred material for medical applications where it is commonly used in implantable devices and other critical equipment.
related articles:
What is the Material of Aluminum PCB?
Komentarze